Pad printing is an indirect printing technique that uses a soft silicone rubber pad to transfer ink between the plate and the product. The ink repellency of the pad on the printing plate and the deinking in the product are important for the stability of the printing quality. We require the pad printing head to draw as much ink as possible on the surface of the steel plate, and transfer the ink as completely as possible on the surface of the product. In fact, it is very difficult to do so, the stickiness of the plastic head itself makes some traces of ink remain on the surface.
The residual ink will cause the printing marks to gradually enlarge and the printing marks to be blurred. In order to avoid the continuous accumulation of the ink layer on the surface of the rubber head, the operator often stops the rubber head cleaning work, which will reduce the production efficiency of the machine, increase the labor intensity of the operator, and affect the stability of the printing quality.
The installation of automatic rubber head cleaning device is an important measure to solve this problem. Some electronic products, auto parts and precision instruments require high precision for printing. In addition to requiring the machine manufacturer to adopt the servo control system, they also need to be on the machine. With the installation of automatic cleaning devices, especially some automated pad printing machines, in order to avoid manual intervention in the printing process as much as possible, the installation of automatic rubber head cleaning devices has become standard.
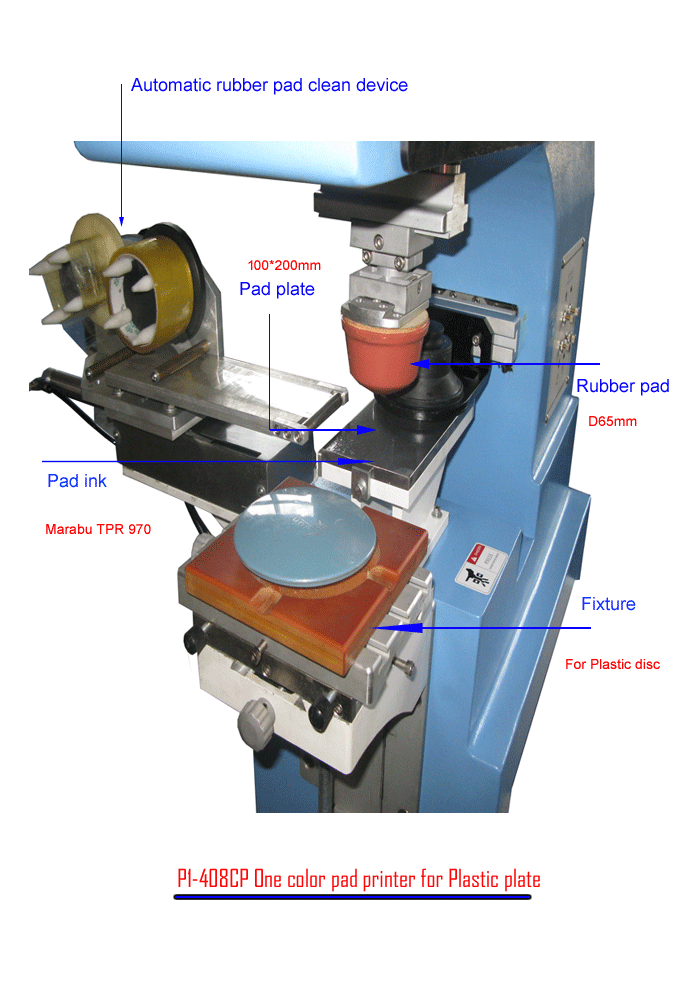