As we all know, polyethylene plastics are not easy to print because inks are not easy to find. However, through our experiments, we still found a special printing for polyethylene plastics, and the adhesion has met customer needs.
It is certainly good that the ink can meet the requirements, but if you have not found the right ink for a while, then it is recommended to take the necessary prepress treatment. But this process is more complicated. You may need to use flame treatment, high frequency treatment or wiping PP to treat the water.
When the adhesion is solved, the choice of the machine is much simpler. Open pad printers, oil cup pad printers, shuttle pad printers, and rotary pad printers are all possible. This needs to be based on customer requirements.
Traditional pad printers need to manually place the product on the fixture, and then remove the product by hand after printing. Such a process requires workers to have a high degree of proficiency and it is difficult to increase the speed. More and more factories use mechanical loading and unloading methods. The pad printing machine of the robot needs to install a rotary platform on the workbench to separate the printing position and the blanking position. Greatly improved printing efficiency, of course, the price of such a pad printer is also relatively expensive.
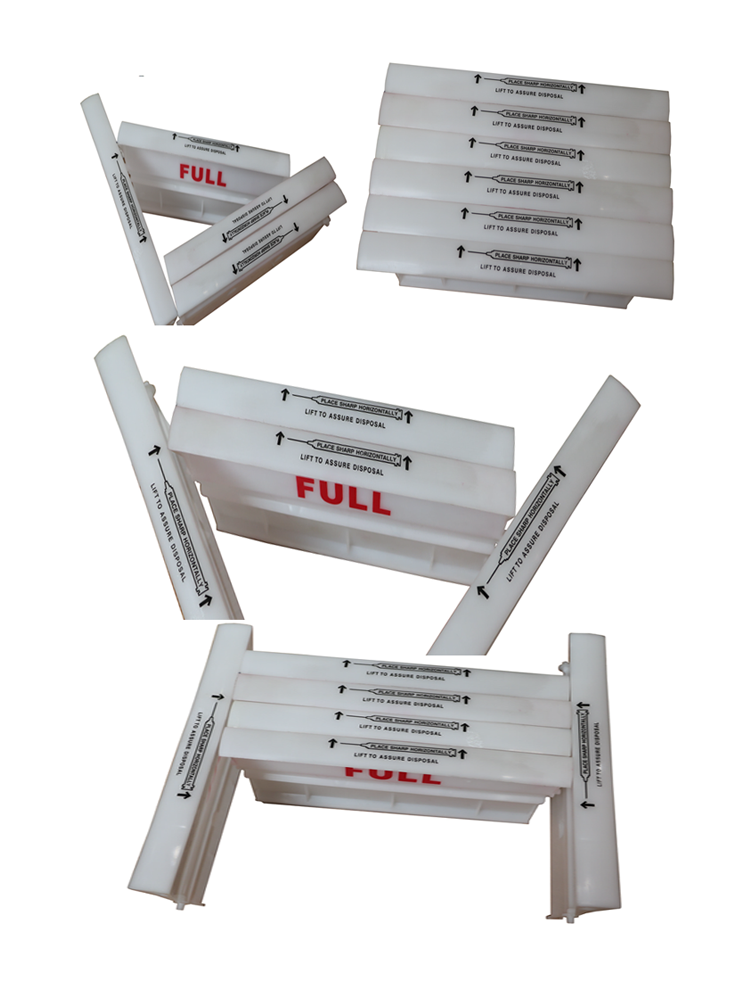