1. Principle of the pad printing process
The pad printing process is divided into the following three processes:
1. Applying ink and scraping ink
The pad printing process uses a planar intaglio plate with the graphic portion below the plate plane. The ink is evenly applied to the surface of the printing plate, and then the ink of the printing plate is scraped off with a hard scraper to leave a graphic ink mark on the pit.
2. Sticky ink
The deformable pad printing head moves to the top of the plate and presses the image at the pit where the plate is stuck and lifts up.
3. The printing and overprinting pad moves to the substrate and presses down to complete the printing, while the overlying device performs the overcoating.
2. Features of the pad printing process:
It can be seen from the process of the pad printing process that the pad printing process has the following characteristics:
Transfer ink using a soft pad printing head. It can be said that the use of pad printing heads is a distinctive feature of the pad printing process and the most important indicator of the pad printing process and other printing processes.
Use a flat gravure. At present, there are mainly two kinds of printing processes using gravure, one is a gravure printing machine which generally prints plastic film, and its printing plate is in the shape of a drum, so the printing speed is very fast, and the plate making method is basically replaced by electronic engraving instead of the traditional etching method. The plate material is mainly made of copper, and the plate is plated with chrome; the gravure used for pad printing is flat, the printing speed is relatively slow, and the plate material is mainly steel. The plate making method still uses the etching method.
The printing ink layer is thin, and the printing substrate is not directly in contact with the surface of the printing plate. Therefore, the printing process is also indirect printing like offset printing. Indirect printing is caused by the transfer of ink through other carriers, and the ink layer is generally thin. . The thickness of the ink layer of the pad printing head is about 10um, which is a difference between pad printing and silk screen printing. It is well known that the thickness of the printing ink layer of the screen printing process makes it widely praised in the printing field, but the pad printing machine The thickness of the ink layer can be increased by multiple printing methods, but this increase is limited and is not conducive to color printing.
More adaptability to substrates. Although screen printing is known as universal printing, in fact, it becomes difficult to print small workpieces and workpieces with larger curvature. Some substrates, such as those with a lower than four-sided or a stepped surface, cannot be printed at all. . On such substrates, the pad printing process shows greater advantages. Pad printing heads can be made into a variety of special shapes to meet complex printing requirements. As we all know, the keyboard of a computer is difficult to print by conventional printing methods. Although the screen printing method can accomplish the task, the printing process is not easy to control. If the combination printing method is adopted by the pad printing process, it will be made. The difficulty of work is greatly reduced. In addition, some cone-shaped substrates are screen-printed to avoid oil return, which must be segmented and printed. It is very troublesome. It can be completed in one time by using the pad printing process. As long as the film film is made to perform the necessary compensation treatment, the degree of deformation can be reduced. lowest.
The pattern is deformed greatly. The ability of the pad to deform and the surface shape of the substrate is an important reason for its ability to adapt to complex substrates. It is also its advantage, and it is also a weakness because it is the main reason for the deformation of printed graphics. The expansion of the network is even more significant. There are two reasons for the deformation: one is that the printing plate text is flat, and the printing is deformed on the substrate that is not flat; the other deformation is related to the deformation of the pad printing head itself. Neither of these deformations can be completely eliminated.
Unbalanced printing pressure. The printing process regards printing pressure, printing speed, printing plate and material properties as the key link affecting the printing quality. It is one of the most important factors in the printing process. Maintaining the equilibrium pressure will result in a print of consistent color stability, but printing. The characteristics of the process determine the shortcomings of its apparently uneven printing pressure. In order to achieve good air discharge, the pad printing head is often designed as a cone-shaped protrusion in the middle, so that the printing pressure shows a characteristic that the circumference is smaller than the middle. In the offset printing process, the difference in printing pressure has a fixed function relationship with the ink layer. In the pad printing process, the functional relationship becomes very complicated, making it difficult to control the printing pressure and finally control the ink thickness.
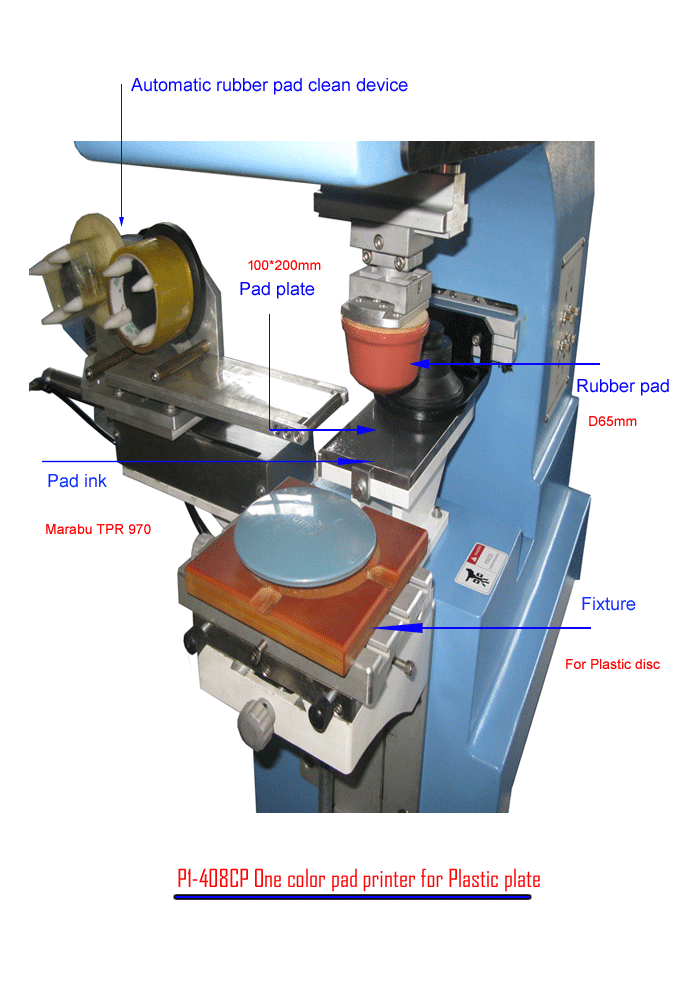