Styles of shuttle pad printer
1 Simultaneous embossing shuttle table pad printing machine
The shuttle pad printing machine originally refers to the pad printing machine with the shuttle type of the work table. The work table of the pad printing machine has multiple printing stop positions. There are two stop positions for two colors, and four stop positions for four colors. The position corresponds to different color plates. When the shuttle table drives the fixture and the product to stay at the set position, the glue head will press down to complete the printing.
This pad printer has the following features:
Multiple glue heads are driven by a cylinder, and the actions of dipping and printing are performed simultaneously. After the rubber head is dipped in ink, it moves to the top of the workpiece, and prints in sequence, and only the rubber head at one printing position transfers the ink, and the other rubber heads are in the idle state. When the machine prints many color books, the ink of the idle running rubber head is easy to dry , affecting deinking.
The distance between the glue heads is fixed, which limits the overall size of the product. In general, this type of pad printer cannot print products with twice the shuttle stroke length. If the outline size is more than double the shuttle formation, another unwanted color is likely to be printed on the product.
At the same time, the shuttle-type pad printing machine is the most common pad printing machine, which is widely used in the printing of various small-sized products such as hardware, electronics, hardware, plastics, and stationery.
Shuttle pad printer with independent drive print head
For multi-color pad printing of some products that are relatively long, or have large dimensions but small printing area, you may want to consider a shuttle pad printing machine with independent pad printing. As the name suggests, the pad printing machines of this type have Different air cylinder controls, the glue head presses down the printing process at different times. Only when the product moves under the glue head, the glue head will perform the printing action, and the actions of each glue head do not affect each other.
This pad printer is suitable for printing long strip products such as chopsticks.
You may also see a storage tray with a diameter of 500mm, to print a two-color logo in the center. Of course, you can choose a single-color pad printer to print one color and one color, or you can choose a pad printer that drives the print head independently , it is done in one go.
The pad printing machine of the shuttle table can actually complete the printing of most plastic products, until more and more customers try to use the pad printing machine to print multi-color logos on some light and soft fabrics.
We know that the edge of the fabric lacks straightness and rigidity, and it is difficult to make a fixture to position it. If the fabric is placed on a shuttle table pad printer for printing, it is difficult to satisfy the color registration. Even if we adjust one of the fabrics to achieve accurate registration, the registration of the next fabric has to start all over again. In fact, the pad printing machine of the shuttle table cannot perform pad printing of continuous cloth, or the quality of pad printing is not uniform.
We had to use another type of shuttle pad printer.
2.Pad printing machine with plastic head shuttle
The rubber head shuttle type pad printing machine is to install a shuttle rubber head in the lateral direction of the rubber head, so that the rubber head performs the left and right shuttle action after dipping the ink to complete the two-color to multi-color printing.
The worktable does not perform shuttle action, it is fixed, so that the position of the fabric remains stationary after being placed on the worktable.
A set of shuttle system is added to the glue head device. The glue head is first dipped in ink above the ink tank, and then moved to the top of the substrate to print the first color, and the glue head shuttles to execute the second color printing.
3.The position where the plastic head shuttles to execute the second color printing is controlled by the photoelectric sensor. It identifies the first color and determines the relative position of the second color to determine the overprinting position of the second color. This method of overprinting avoids the disadvantages of inaccurate overprinting caused by the use of jigs or uneven edges of the fabric for positioning.
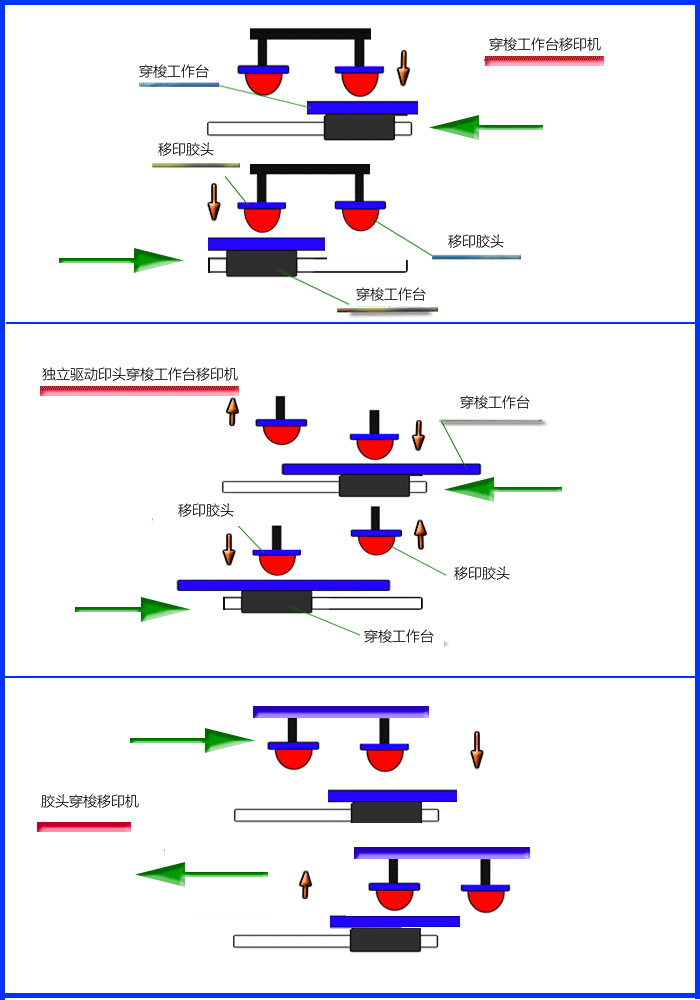